Join our team
For 50 years, Delta Systems has been a symbol for engineering excellence, providing the outdoor power equipment and adjacent industries with the highest quality, most reliable, and safest products. We build innovative parts that are tough, withstand unforgiving conditions and persevere through daily use and wear. Our world-class product quality ensures each item that leaves our dock will perform as expected, when expected. In fact, our customers partner with us because they trust and depend on what we deliver:
True quality that never quits.
Driving this dedication is the elite force that defines the Delta Systems team. We come to work every day because we want to design better, build stronger, and expertly craft world-class solutions that make people happier and keep them out of harm’s way. We are proud of our quality work!
Learn & Grow at Delta Systems
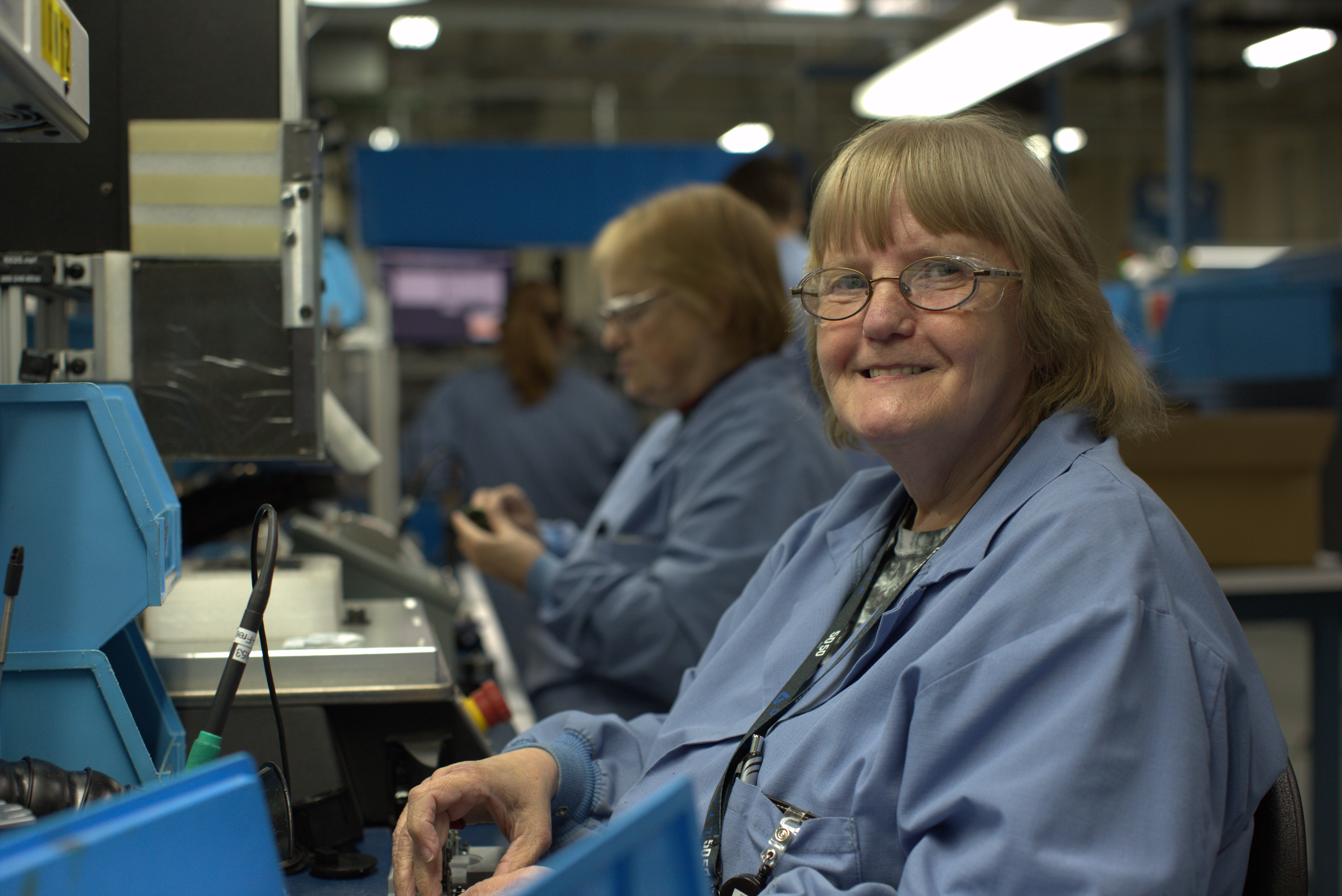